漁業文化が息づく富山県氷見市を拠点に、フィッシュレザーの製造を行う株式会社シンクシー。「生命の恵みを無駄にしない持続可能なものづくり」を大切にしたフィッシュレザーづくりを行っているというが、魚の皮をどのようにしてレザー生地にしているのだろうか。
今回は株式会社シンクシー代表の野口 朋寿さんにフィッシュレザー開発の背景や、環境に配慮したものづくりについて話を聞いた。
PROFILE|プロフィール
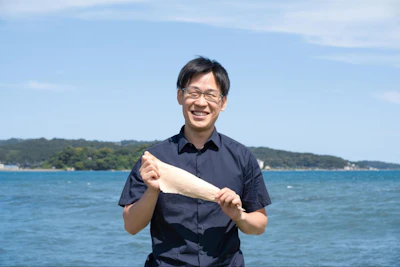
野口 朋寿
株式会社シンクシー 代表
1993年、香川県出身。 2016年、富山大学芸術文化学部卒。
子供のころから魚が好き で、大学時にフィッシュレザーの研究を始める。 2018年、富山県氷見市地域おこし協力隊としてまちづくりに関わりながらフィッシュレザーの事業化を目指す。2020年にブランド「tototo」を立ち上げ、2022年に株式会社シンクシーを設立。
魚の廃棄物を有効活用したい
まずは、フィッシュレザーに着目した背景について教えてください。
私が芸術文化学部に在籍していたときに、伝統工芸の漆の勉強をしていたことから、牛皮などに漆を塗って、新しい表現方法を模索していました。そこで、もともと魚が好きだったこともあり、魚の皮に漆を塗ってどんな表現ができるか試してみようと思ったのがきっかけでした。そのような実験を行うなかで魚屋さんに皮を貰いにいくと、バケツから溢れるほどの皮をいただくこともあり、その廃棄量の多さにとても驚きました。
魚は寿司などで身だけを食べる場合、頭や内臓、皮といった部位は捨てられることが多く、実は魚1匹のうち半分ぐらいが廃棄部分になります。現状、魚の廃棄物の約91%は焼却処分され、残りの約9%が動物の餌や畑の肥料として利用されています。特に日本では多くの魚が消費されているため廃棄される量も多く、その皮を加工することで活用できないかと考えたのです。
この記事は会員限定です。
登録すると続きをお読みいただけます。 会員登録でできること
- 会員限定記事の閲覧、
音声読み上げ機能が利用可能 - お気に入り保存、
閲覧履歴表示が無制限 - 会員限定のイベント参加
- メールマガジン配信で
最新情報をGET